AWHU-5/AWHU-8
AWHU-5/AWHU-8
These gauges can be used in temperature up to 800°C for both static and dynamic measurement. However, owing to the construction of the sensing element, measurement is recommended in temperature at 600°C or above. The sensing part has half bridge configuration with active element and dummy element, and it is measured in full bridge method using the attached temperature compensation circuit board. Since these gauges have small backings and thin sleeves and cables as standard specifications, they are applicable to narrow and/or curved areas.
Main object material | Metal |
---|---|
Operational temperature | -196 to +800℃ |
Temperature compensation range | RT to +800℃ |
Bonding adhesive | Spot welding (TML spot welder W-50R is required) |
Backing | Inconel 600 |
Element | Special alloy |
Strain limit | 1%(10000×10-6 strain) |
Fatigue life at room temperature | 1×106(±1000×10-6 strain) |
-
Specifications
Type A B C AWHU-5 3 10 22 AWHU-8 3 16 16 Type Gauge
length
(mm)Gauge base Test specimen Resistance in (Ω) Dimensions (mm) Materials AWHU-5-9AKM-2(6F)-12.7 5 L10×W3×T0.8 Inconel 600 Inconel 600 equivalent 60 AWHU-8-9AKM-2(6F)-12.7 8 L16×W3×T0.8 120 *Each package contains one strain gauge.
*Other cable length available on request
(Made to order by every 1 m for MI cable and by every 0.5 m for vinyl cable)
Automotive Measurement System FAQ
Automotive FAQ
Wireless communication measurement system
Datamail Management Software TDS-Mail
Datamail Management Software TDS-Mail
This software transmits measurement data from static strainmeters (T-ZACCS3 TS-360, TDS-150, TC-32K, TC-31K, MD-111, TC-35N) using interval timers, etc. via e-mail (data mail) using a data mail converter. This software receives it and performs recording and alarm monitoring. Remote monitoring is easily achieved without the need to build a large server system.
- Features
- Telemetry system with low running costs
- Supports 5 target locations (measuring instruments)
- Data acquisition is possible at multiple locations as long as an e-mail receiving environment is available
- No need to manage servers, which are difficult to maintain
- Sends alarm e-mails and data absence e-mails
- Optional functions include rainfall measurement, quadrature calculation, multistage inclinometer, and horizontal displacement measurement
-
System Configuration
OS / PC / communication environment / protection key
OS Microsoft Windows 7(SP1)/8.1/10/11 PC CPU and CD drive recommended by the above OS environment and dual core or higher
HDD space: The above OS environment recommends the following disk space and the following space is required for setup.- This software: 12 MB of available space or more
- Microsoft .NET Framework 4.8 : 4.5 GB
communication environment Internet connection environmentEmail can be sent and received Protection key USB Dongle
Application image
TDS-Mail automatically converts measurement data from measuring instruments installed at various measuring points into e-mails and transmits them.
TDS-Mail data mail management software extracts and records measurement data from the received mail and monitors alarms.
*“FOMA”, the 3rd generation mobile communication system, will terminate its service on 2026/3/31.
Please be careful if you are using FOMA network compatible model FPT-Em/DMA-S/DMA-ES.
Option
Inclinometer and rainfall option version TDS-Mail-F
- Rainfall Measurement
Rainfall measurement is made possible by counting the contact pulse signal from the tipping rain gauge using the NSW-01C network module or the built-in contact input of the MD-111 monitoring system controller.
The total rainfall, hourly rainfall, and 24-hour rainfall are calculated from the rainfall counts.
- Quadrature Calculation
Four-Way Calculation Using Measurement Channel Data
- Multi-stage inclinometer - horizontal displacement measurement
Extended data can be created for each borehole and horizontal displacement distribution graphs can be displayed
More Information
Bivalve shell body motion measuring device SL-200 series
For multi-recorder
For multi-recorder
The following options are available for the multi-recorder
-
Multi-Recorder Options
- Multi-Recorder Measurement and Data Processing Software
- Multi-Recorder Measurement and Data Processing Software Visual LOG TMR-7630
Software for multi-channel dynamic measurement and data processing. - Bridge Box SB-120T / SB-350T
- Bridge box for strain 1G/2G/4G units TMR-222/TMR-322.
- Handle TMR-HDL
- Handle for carrying and fixing. (Special screws included)
- Bracket TMR-BKT
- L-fittings for installation. (Special screws included)
- TMR display unit adsorption stand
- A stand with suction cups to fix TMR-381/-281 display units to glass surfaces, etc.
- TMR display unit fixed stand
- This stand secures the TMR-381/-281 display unit to the control unit at any angle.
- Display unit connection cable CR-6442
- Used for extension between TMR-211 and TMR-281 (1.5m)
-
Analytical Method One-dimensional frequency analysis
Maximum and minimum value method, maximum and minimum value method, time method, amplitude method, level crossing method, rainflow methodNumber of Analyse 16 analyses (for 1 ms sampling, arbitrary CH)
80 analyses (for 10 ms sampling, max/min method only)Number of slices Maximum ±50 (100) arbitrary setting
More Information
Attenuator cable
Attenuator cable
Used when measuring voltage with a DC dynamic strainmeter.
-
CR-4010, CR-4020
Cable to connect to the ultra-compact dynamic strain recorder DC-204R and the multi-recorders TMR-321 and TMR-221.
Type Attenuation Length(m) Cable ends CR-4010 1/1000 1.5 BNC Connector
Plug for ultra-compact dynamic strain recorder and multi-recorder (PRC07-P8M)CR-4020 1/100 -
CR-4110, CR-4120
Cable to be connected to dynamic strainmeters DC-004P and DH-14A
Type Attenuation Length (m) Cable ends CR-4110 1/1000 1.5 BNC Connector
NDIS plug (PRC03-12A10-7M)CR-4120 1/100
Digital dynamic strainmeter DRA-162B
Digital dynamic strainmeter DRA-162B
This carrier wave type dynamic strainmeter is designed for on-line measurement using a personal computer.
Input waveforms are continuously digitized, recorded in the internal memory, and transferred to a PC.
Since dynamic phenomena can be captured numerically, data analysis using a PC is easily possible.
Equipped with a data memory of 256k words/channel, data trigger start and pre-trigger recording are also possible.
It also provides analog outputs similar to those of ordinary dynamic strainmeters.
All operations are performed from a PC via a LAN interface.
In addition to strain gage and strain gage transducers, voltage measurement is also available.
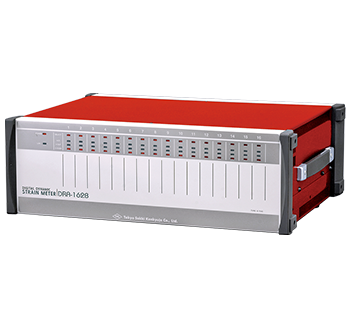
- Features
- Built-in 16-bit A/D converter for each channel, waveform recording by digital value
- Built-in 256k words/channel data memory (for 16 channels)
- Remote sensing of bridge voltage minimizes sensitivity degradation during cable extension (up to 100 m)
- Each setting can be PC-controlled
- Data backup possible on the main unit of the instrument
- Bridge voltage switching (0.5 VAC, 2 VAC) can be set independently for each channel
- Built-in check functions (sensitivity, input open, over, insulation)
- Capable of transferring recorded binary data over a LAN at a rate of approx. 500 kwords/second
- TEDS sensor data readable
- Card-type internal configuration for easy maintenance
- Synchronous measurement is possible with up to 16 units (256 channels) connected
- DRA-7162 acquisition software is included as standard equipment.
-
Features
Type DRA-162B Measuring object Strain gauge, strain gauge transducer
DC voltageNumber of channels 16 channels Measuring range ±32,000×10-6 strain
(Gage factor fixed at 2.00)Frequency response DC to 2.5kHz External dimensions 428(W)×148(H)×320(D)mm Weight Approx. 11kg Power supply AC100-240V 50/60Hz
130VA MAX